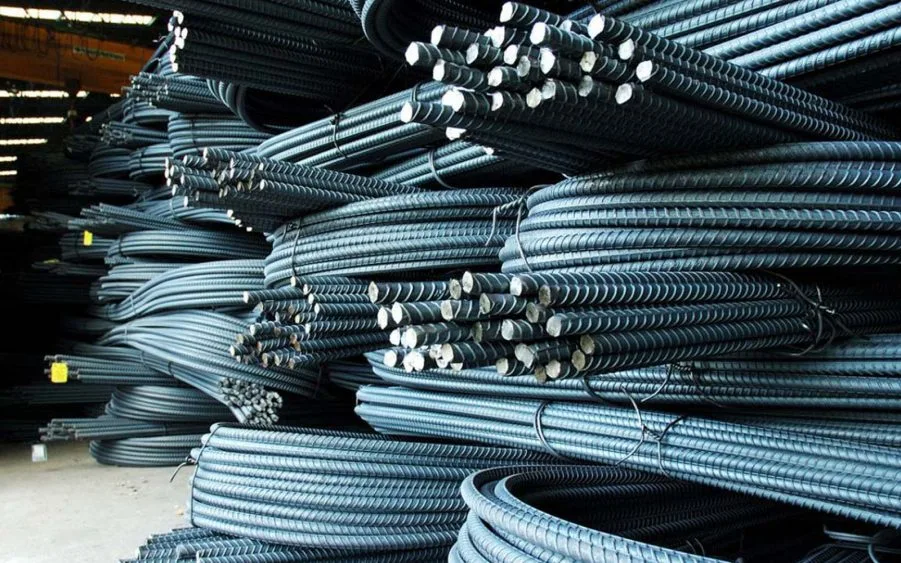
Steel is globally recognised as an ingredient for the actualisation of sustainable industrial and economic development aspirations of nations.
Steel is a high-strength, formable, versatile and low-cost material used globally for a variety of purposes. It is used in the production of automobiles, building and infrastructure construction, domestic appliances, fabrication of metal products, agriculture and military equipment and construction of energy, rails and road facilities.
Global steel production grew significantly from 28 million metric tonnes (mt) at the beginning of the 20th century to 781 million mt at the end of the century. Over the 20th century, production of crude steel rose significantly to 1.6 billion mt per year. Also, during this period, the consumption of steel increased at an average annual rate of 3.3 per cent of global steel output.
With the opening up of global trade after the COVID-19 disruptions, Africa, as of February 2022 has produced 1.3 million mt, mostly from Egypt, South Africa and Libya. Though Nigeria is blessed with abundant natural and human resources, Sadly, however, the country is yet to fully exploit the potential in the steel sector.
In a chat with Science Nigeria, the chairman, basic metal, fabricated iron and steel products, Manufacturers Association of Nigeria (MAN), Dr. Kamor Yusuf, pointed out that Nigeria is blessed with all the major raw materials needed for the production of iron and steel. He added that these include 3 billion mt of iron ore, 3 billion mt of coal, more than 700 million mt of limestone and 187 billion SCF of natural gas.
Giving a background of steel development in Nigeria, he said the planning for the Nigerian steel sector started in 1958. However, after about 50 years, the country is yet to establish a stable iron and steel sector despite the huge investment of over $7billion already expended on steel development.
“The exploration started at the Itakpe iron ore deposits in 1963. Between 1961 and 1965, several foreign companies who came to assess the Nigerian steel sector reported that steel production was not feasible as a result of lack of domestic market, high cost of the technology, infrastructural development, lack of manpower, the poor grade of iron ore deposits in Nigeria and other international political considerations. However, in 1967, Russian experts came to Nigeria to conduct feasibility studies toward the establishment of an iron and steel plant in Nigeria.
“During the period 1960 – 1970, the Federal Government directly coordinated the iron and steel sector in Nigeria and there are instances of policy inconsistency. During the 2nd National Development Plan (1970 – 1974), the government established the National Steel Development Authority (NSDA) which was saddled with the responsibility of iron and steel development in Nigeria. Under the coordination of the Russian experts, NSDA conducted various geological surveys that led to the discovery of commercial quantities of iron ore in Nigeria and during the implementation of the third National Development Plan (1975 – 1980), the government signed various agreements for the construction of two integrated steel plants and three rolling mills.
“In 1979, the government promulgated Decree No. 60 of September 18, 1979, which unbundled NSDA and established the Ajaokuta Steel Company, Delta Steel Company, Jos Steel Rolling Company, Katsina Steel Rolling Company, Oshogbo Steel Rolling Company, National Iron Ore Mining Company, National Steel Raw Materials Exploration Agency, National Metallurgical Development Center and the Metallurgical Training Institute. While the three rolling mills and DSC were completed on schedule, the ASC was not completed after over 40 years of intermittent construction work. Till today, the Ajaokuta Steel Company (ASC) has failed to take off while the Delta Steel Company (DSC) and the rolling mills in Oshogbo, Jos and Katsina are producing at very low capacity utilisation,” he said.
Yusuf said these developments have led to fluctuations in the production value added and capacity utilisation in the base metal, iron and steel sector of the economy.
He added that several studies indicated that the Nigerian Steel Sector is being sustained through the recycling of scrap steel obtained mostly from municipal solid wastes. In many rolling mills, 100 per cent of scrap steel is recycled for the production of iron bars used for civil construction. Scrap steel recycling results in the generation of <7 per cent and 7-15 per cent slag for iron and high carbon respectively.
“The sector is also highly dependent on imported billets. However, as a result of the high cost of billet importation, many steel companies are unable to function. Nigeria imported $1.18 billion worth of steel materials in 2020 according to the United Nations COMTRADE database on international trade. From the statistics available from the National Bureau of Statistics (NBS), Nigeria imported iron, steel and metals, valued at N837.76billion in the 3rd and 4th quarters of 2021. According to the statistics, the country imported basic metals, iron and steel products with 600mm in width, rolled, painted and coated, varnished and coated with plastics within the 6 months. The total value of basic metals imported within the two quarters was N748.529 billion while that of Iron and Steel was N88.232 billion,” he added.
Speaking in an exclusive chat with Science Nigeria, the director-general of the Raw Materials Research and Development Council (RMRDC), Prof. Hussaini Ibrahim, pointed out that the Nigerian steel sector is facing a lot of operational challenges.
He maintained that the privatisation that was carried out in 2004 – 2005 failed to revive the sector, noting that the two integrated iron and steel companies were unable to produce billets for the 20 steel rolling mills which include private sector establishments in the country.
“Following the privatisation exercise, the DSC started operations in December 2005 after about 10 years of inactivity. Although, during the third national development plan (1975 – 1980), thousands of Nigerians were trained in-country, and India, Russia, Germany, the UK, Japan, etc. Unfortunately, when the public steel sectors collapsed, the staff was left in limbo for a long time, which resulted in the accumulation of huge pension liabilities. These huge pension liabilities made the steel companies attract fewer premiums during the privatisation exercise.
“Likewise, the location of most of the steel projects made their operations costly. Iron was being mined at NIOMCO, Itakpe in the north-central part of Nigeria. It was being sent to DSC down south for the production of billets, a distance of 327km by rail. Billets produced from DSC were sent to the three inland rolling mills, one in southwestern Nigeria (Oshogbo), another in north-central (Jos) and the third in northwest (Katsina), all these locations are far from Aladja from where the billets were produced. Another challenge is that of funding/operational cost. After the successful construction of DSC, NIOMCO folded up, DSC followed and because of lack of billets, the other three government-owned rolling plants also folded up,” he said.
The RMRDC boss highlighted that the consequences of the sub-optimal operation in the steel sector are many.
He added that apart from the foreign exchange drain, if the phase 1 of the Ajaokuta steel had been completed and completely installed and operational, the multiplier effect would have been enormous including direct employment of 10,000 workers at the plant, 20,000 in the raw materials industries and 30,000 workers in downstream industries utilizing iron and steel products. Also, the conservation of foreign exchange for the importation of steel products on annual basis.
“If the sector is functioning adequately, it will also contribute no less than 30 per cent of the inputs required in the automotive industry in Nigeria. Likewise, the plant can meet most of the national requirements for chemicals.
“The success of local fabrication and production of process equipment and universal components also largely depends on the optimal operation of the companies in the sector. Presently several process equipment designed and fabricated locally cannot be replicated given the high cost of imported steel products. This has seriously limited local production of equipment for the cottage, small and medium enterprises and the dearth of universal components and spare parts required in the manufacturing sector, leading in most instances to downtime of equipment in several manufacturing industries.”
“One notable achievement worthy of mention was that in 1994/95 Nigerian scientists, engineers and technologists teamed up to develop a process of upgrading the Itakpe iron ore to the super concentrate (65/67 per cent) grade required for finished without the addition of foreign inputs. This development led to the production of the first all Nigeria steel, the iron ore of which hitherto had to be imported at colossal foreign exchange.
“This effort was discontinued as iron and steel sector was not properly funded. For more breakthroughs to be recorded locally in the sector, the Raw Materials Research and Development Council is promoting synergy among the government, industry, academia and the private sector. Along this line, human capacity building, research and development in the metallurgical industry particularly the iron and steel sector should be given the serious attention it deserves by the Federal Government,” he added.