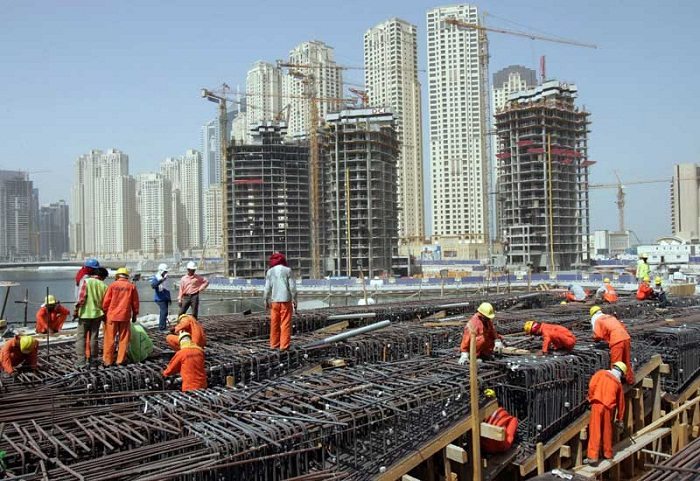
The building and construction industry is one of the most important sectors of any economy. The significance of this industry is often measured by its contribution to the gross domestic product (GDP).
In Nigeria, with the abundance of basic building materials such as clay, laterite, stone, lime, agro-industrial waste, wood/timber, granite, various types of sand (including glass sand) in their natural state, the contribution of this sector to the GDP is expected to be high and significant. However, the sector contributes only 30 per cent of the GDP which is far less than 70 per cent recommended by the World Bank.
To facilitate and increase activities in the sector and tackle Nigeria’s housing deficit, the Federal Government initiated the National Integrated Infrastructure Master Plan, (NIIMP), a 30-year infrastructure plan with a target date of 2043. The plan aims to bring Nigeria’s infrastructure stock to the 70 per cent of GDP level.
The NIIPM is expected to mitigate the current housing deficit of 17 million houses by building a minimum of 700,000 houses per year instead of the current 2,000 houses built annually.
Similarly, government also waived the initial 10 per cent payments on mortgages below N5 million provided by the Federal Mortgage Bank, in its bid to support the mortgage industry.
As a result of the intervention by the Federal Government, residential construction industry in value terms increased at a compound annual growth rate (CAGR) of 4.2 per cent during 2015-2019.
Meanwhile, the building and construction industry is expected to record a CAGR of 13.9 per cent to reach NGN 10671.3 billion by 2024 while the commercial building construction market in value terms is also expected to record a CAGR of 12.5 per cent by 2024
Speaking exclusively to Science Nigeria, a building engineer, Engr. Chukwugozie Okeke, lauded several government initiatives to drive down construction costs and tackle the country’s building deficit.
He added that one of the major ways the country can reduce the high cost of conventional construction materials such as concrete, cement and steel, is to promote the use of alternative construction materials.
Okeke reasoned that at the global level, different solid wastes generated in large quantities are used as full or partial replacements for conventional materials in many developed countries. “For instance, ashes from industrial and agricultural wastes such as fly ash and rice husk ash are used as ‘pozzolan’ to partially replace cement in concrete production,” he said.
The expert noted that although there are no commercially viable alternatives, presently, efforts are being made globally to replace cement as much as possible with a number of alternative materials. These include supplementary cementitious materials (SCMs), mineral admixtures or pozzolans. Use of these materials lowers the embodied energy of the concrete and offset almost one tonne of carbon emissions for every tonne of cement replaced. Most of the alternative materials are cheap and are abundantly available. They also do not compromise strength and durability properties of the concrete.
Speaking in the same vein, an environmentalist, Adakole James, explained that among the SCMs are agricultural wastes such as rice husk ash (RHA) which contains amorphous silica similar to that found in most natural pozzolanic materials.
“RHA concrete has shown superior performance over normal concrete. Presence of RHA as partial substitute of cement has been reported to enhance workability, improved strength, increase durability and reduce shrinkage among other enhanced properties. In Nigeria, more than 160 million tonnes of rice husk is produced annually. Closely allied with this is sugar cane straw ash (SCSA) which also exhibit same chemical and physical properties as the RHA. Performance of concrete containing a fraction of SCSA as substitute for cement has been extensively investigated. Recycling SCSA in this form will rescue the environment from the pollution caused by huge amounts of sugar cane straw produced annually.
“Research also shows that the structural behaviour of reinforced palm kernel shell concrete (PKSC), has lower density (24 per cent of normal concrete), increased compressive strength (14 per cent higher), with lower modulus of elasticity and flexural strength which were 33 per cent and 15 per cent of normal weight concrete (NWC), respectively. In addition, bamboo is a very strong fibre that is used as reinforcing material. The compressive strength of bamboo is two times higher than that of concrete, while the tensile strength is close to that of steel,” he stated.
Listing interventions at making use of local materials to reduce cost of building materials in Nigeria, the director-general, Nigerian Building and Road Research Institute (NBRRI), Prof. Samson Duna said the council has launched cement-stabilised bricks technology.
According to him, the use of the material reduced the cost of construction drastically.
“NBRRI has also developed building materials like pozzolana, mardotile roofing and varieties of machines for their production. The products reduce the cost of production of mortar and concrete, reduce heat of hydration and reduction on effects of alkali aggregate reactivity,” he added.

Speaking to our correspondent, the director-general, Raw Materials Research and Development Council (RMRDC), Prof. Hussaini Ibrahim, said the council is presently collaborating with the New Material Nigeria Company Limited, a member of the China National Building Materials Group (CNBM) wholly owned by the government of China which has introduced a new innovative construction material known as ‘fibre cement board’ into the Nigerian market.
According to him, this makes Nigeria the first country outside China where an alternative to gypsum board is being manufactured.
“The fibre cement board is resistant to weather, water and fire. It is sound proof, shatter resistant, flexible, termite-resistant and costs lower than normal bricks. The fibre cement board is made out of a composite of cement, cellulose fibres like paper pulp, quartz and sand. They are used in building construction of walls, partitioning, roofing and flooring. It can be used for internal wall partitioning as well as exterior wall cladding.
“As good insulators of heat and sound, they are preferred to the solid cement block or bricks commonly used. The locally produced fibre cement board provides an alternative to gypsum board and mitigates capital flight, as $132million worth of gypsum is imported annually into the country,” he said.
The RMRDC boss further said that, more recently, the council initiated collaboration with Ifrique Eco Solutions towards producing eco-interlocking tiles.
He posited that the tiles are made out of low-density poly ethylene (LDPE) such as waste ‘pure water’ sachet, bin bags, wrap plastic and almost all other polythene bags. Ibrahim pointed out that they can also be made from polyethylene terephthalate (PET) or plastic bottles.
“The focus of the present work is on the use of plastic bags, as plastic bottles are being reused for other purposes. The process is simple and consists mostly of cleaning, melting, mixing with sand and other materials such as colorants, etc. and setting. The council is working towards fabricating the equipment already design for industrial production of the product,” he said.
The DG also said the council, in addition, is working with Ifrique Eco Solutions on upcycling discarded PET bottles to building bricks. This project provides an opportunity for the country to showcase its eco-friendly credentials and aligned with the Sustainable Development Goals (SDG) and circular economic principles.
He stated that it isstrongly believed that the PET sand bottle buildings would revolutionise housing construction in Nigeria. It would also help to create a lot of direct and indirect jobs, in addition to keeping the environment clean.
“These initiatives will substantially reduce the price of building raw materials in Nigeria. Also, they will save the nation more than N2trillion on annual basis in foreign exchange equivalent if the projects are commercialised. It is envisaged that the production of building materials from locally available raw materials will generate more than 50,000 jobs in the country and make building of houses easier for the local populace. These will facilitate increase in the contribution of the sector to GDP, in line with the dictates of the World Health Organisation.
“For these initiatives to be maintained and sustained, the government as a matter of urgency must create appropriate means for delineation and implementation of research results. In addition, there is need for a policy that will enhance private-sector participation in the commercialisation of these research efforts. This will significantly reduce the cost of building and construction locally,” he added.